Grizzly Feeders
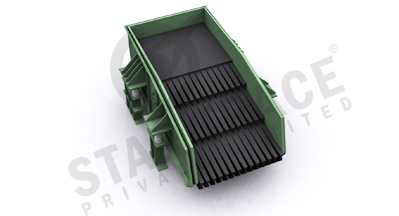
STAR TRACE Grizzly Feeders have greater versatility and adaptability for the increase in production/products. The rugged design and construction smooth vibrating mechanism helps in reliable operation, long durability and helps to lower maintenance costs. It is suitable for continuous, uniform feeding of raw material into the crusher and equipment while screening plants of Mineral & Mining Industry, Construction materials, Silicate, Power sector, Steel sector, Cement Industry, Chemical Industry and Foundries etc.
- A robustly constructed range of vibratory machines extending from units 0.5m widex2m longup to units 1.5mx4.5m.
- The grizzly feeders are intended primarily for use ahead of primary crushers are designed to handle large run-of-quarry stone, take the impact of dumped loads and smooth out the flow of materials to the crusher.
- All models of grizzly vibro feeders have a flat reinforced impact area followed by a sloping grizzly bar section.
- The longer grizzly feeders are fitted with two stepped, grizzly bar sets. Replaceable wear sections of mild steel, manganese steel or rubber are fitted depending on the duty specified.
During material dewatering, water is filtered through the mesh as a result of vibration while the material is conveyed toward the point of discharge. The filtered water carries solid particles whose size is slightly smaller than the mesh openings, which must be recovered by means of hydrocycloning and incorporated to final product in the discharge area. The level of moisture that can be obtained in the end product is between 10% and 15%, depending on its nature, particle size distribution and water content in the feed materials.
When the two vibrating motor that installed vertically on the sieve relatively rotate, the eccentric block of two vibrating motors produce rated excitation force. The horizontal excitation force cancel each other out, the vertical excitation force is transported to the whole screen surface through the body mass vibration. Materials do the jumping movement on the screen surface to the outlet because of the vertical excitation force. Materials which smaller than the mesh drop into the lower layer and discharge from the outlet after doing the jumping movement. Because of the reasonable screen, after vibrating screen, we can get materials of different concentration particle sizes and done the rating work of materials.
Vibrating feeders consists of vibrating frame, spring, vibrator, motor vibrating device and motor. The vibrator is made of two fixed eccentric shafts whose gears are jogged. When installation, the two gears must be jogged according to the sign. Through drive of the motor, the two eccentric shafts start rotating to produce a linear huge power which forces the feeder to vibrate. Through the vibration, the materials will slip and sling on the funnel, moving forward, when the materials pass the screening part, smaller parts will fall down, and avoiding the further crushing, so screening purpose can be reached.
- The Grizzly feeder is suitable to feed primary jaw crushers, selecting the large sizes which require primary crushing, the smaller sizes and any fines which must be eventually rejected.
- The Grizzly vibro feeder consists of a very large vibrating body made of thick plate with inside lining of anti-abrasive plate. The Grizzly vibro feeder is driven by two or four vibrating motors. The vibro feeder(which may either be placed on a steel or concrete base) rests on spring.
The area needed for the Grizzly Bar Section may be calculated from the following empirical formula and tables. The resulting figure provides a guide to the Grizzly Feeder model required.
Grizzly Bar area (m2) = Tonnes per hour of under size
Capacity/m2 A x Factor B x Factor C
- Grizzly Feeder may be supplied complete with Variable Feed Rate Controllers. They incorporate the very latest frequency inverter technology for applications that require frequent adjustment of the feed rate.
- For other applications twin vibrator phase reversal braking starters which enable the unit to stop within seconds may be suitable. The number of stop/ starts that may be made per hour is limited depending upon conditions.
- Consult us about your Electrical Control Equipment requirements.
- Power
- Mining
- Aggregates
- Recycling
- Concrete
- Quarries